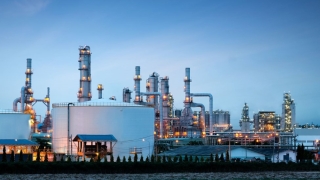
This journey covers some essential and fundamental concepts of automatic control of continuous process, which includes the in-batch control of batch processes. It is aimed to provide:
- Practice-oriented context and conceptual support for a chemical engineering first course in process control, and
- Information for a practitioner needing to independently learn the essentials.
Here is an outline of current (with author's name) and planned (no name yet) topics. If you know of a topic that should be added, have a web URL or a topic, or have any comments on the postings, send a note to russ@r3eda.com.
Outline of an application-oriented view of process control essentials
- Overview
- Processes and Process Characteristics - Russ Rhinehart
- Process Control is Inventory Control - Russ Rhinehart
- Deviation Variables - Planned
- ISA Process Control Terminology, Symbology, and Standards - Planned
- PI&D
- Understanding P, I, & D – Russ Rhinehart
- PI&D Explained - Jacques Smuts
- Understanding Laplace representations in process control - Russ Rhinehart
- Unraveling Laplace Notation for PID - Jacques Smuts
- PID Controller variations - Russ Rhinehart
- Bumpless Transfer and Tuning – Jacques Smuts
- Integral Windup and velocity mode – Doug Cooper
- PID controlled process simulators - Planned
- How Process Characteristics Shape Controller Choices
- Process Characteristics and Choice of P, I, D functions - Planned
- Noise & Filtering
- “Noise” types (Normal, Autocorrelated, Spurious Events, Discretization) - Planned
- Filters – MA, FO, anti-aliasing, set point - Jacques Smuts
- Noise and filters First-order filter, and some analysis – Russ Rhinehart
- Statistical Filter - Russ Rhinehart
- Simulators of Noise and Filtering - Planned
- Controller Tuning
- Goodness of Control Metrics, Goodness Criteria for Tuning, Heuristic PID Tuning I & II - Russ Rhinehart
- PID Tuning III - Planned
- Cohen-Coon Tuning - Jacques Smuts
- Minimum IAE Tuning - Jacques Smuts
- Design of Sensors and Final Elements
- Valve characteristic Responses - Russ Rhinehart
- Valve Problems - Jacques Smuts
- Orifice Calibration - Russ Rhinehart
- Cavitation in Orifices and Valves - Planned
- Valve Design (size, capacity, expander/reducer, characteristic, actuator) - Planned
- Sensor and Final Element Effects on Pressure Loss and Pump Sizing - Planned
- Transducers – analog and digital, and calibration and discretization - Planned
- Instrument issues (rangeability, precision, noise, signal discretization) - Planned
- Communication
- Measurements, Scaled Variables, and Issues - Russ Rhinehart
- Scaled Signals and Conversions – Doug Cooper
- Lines on the PFD/EFD and P&ID - Russ Rhinehart
- Modeling
- FOPDT Modeling by Empirical Methods - Russ Rhinehart
- Regression software to generate models from empirical data - Planned
- FOPDT Modeling from First Principles - Russ Rhinehart
- The Fortunate Insensitivity of Control to Model Perfection - Planned
- Classic Advanced Regulatory Control
- Gain Scheduling – Doug Cooper
- Output Characterization - Russ Rhinehart
- Output Characterization Application - control valve inverse - Jacques Smuts
- Override and erf - Russ Rhinehart
- Ratio and Scaled Signal Calculations - Russ Rhinehart
- Ratio Control the right and wrong approach - Jacques Smuts
- Cascade - Jacques Smuts
- Cascade - Russ Rhinehart
- Feedforward - Doug Cooper & Allen Houtz
- Feedforward - Russ Rhinehart
- Interaction and Solutions – RGA pairing, detuning of less critical, one-way and two-way decouplers - Planned
Process Control is Inventory Control
You change the inventory of heat to change temperature. You change the inventory of material to change level. Understanding how the inventory relates to the controlled variable is...
See MorePID Explained
A qualitative explanation of P, I, & D actions using graphs.
See MoreUnderstanding P, I, and D
Understanding what the proportional, integral, and derivative terms do within the PID controller is essential to choose appropriate action, trouble shoot controllers, chose appropriate...
See MorePID Controller Variations
It is important to understand the variations on the PID algorithm when tuning and when choosing a version that is consistent within your use context. Unfortunately, there are many names for...
See MoreBumpless Transfer and Tuning
Switching from MAN to AUTO mode or LOCAL to CASCADE or changing the controller integral time should not cause a change in the controller output, a bump. But a primitive coding of the PID...
See MoreIntegral Wind-Up and Solution
What is integral wind-up and how velocity mode solves it.
See MoreTuning PID Controllers
Tuning controllers is the procedure for choosing the coefficient values for the P, I and D modes. It must be simple to execute, fast, and non-disruptive to the operating process. Heuristic...
See MoreCohen-Coon Tuning
A procedure and commentary on this tuning approach that includes deadtime.
See MoreMin IAE Tuning
Procedure and Commentary on tuning for minimum Integral of the Absolute Error
See MoreNo! Not Laplace Transforms
In my 13-year industrial career, I never used Laplace transforms. However, transfer functions and block diagram notation are efficient methods to describe dynamic behaviors, and are often...
See MoreDecoding a Laplace Representation of a Controller
A how to relate the Laplace notation to the PID controller variation and features
See MoreFOPDT Models from Skyline Inputs
The classic textbook method to generate FOPDT models is the reaction curve technique, a pre-computer era technique: Start from a steady state, make a step and hold in the controller output...
See MoreUse First-Principles Modeling to Get FOPDT Coefficient Values
Conventionally, we obtain model coefficient values by open-loop step-testing of the process; but this creates undesirable process upsets, and only reveals the local process behavior. This...
See MoreUnderstanding Valve Flow Characteristics
The response of flow rate through a control valve depends on the friction losses in the piping in which it is installed as well as the controller signal. The installed characteristic (a...
See MoreOrifice Calibration
The ISO method for orifice design and calibration is grounded in the ideal square-root relation between pressure drop and flow rate, specifies the in-pipe structure for an orifice, and...
See MoreMeasurements, Transmission Signals, and Issues
This is an introduction to scaled information transmission signals (for example 4-20 mA, 3-15 psig, etc.), the actual sensed signals (like using orifice dP to infer flow rate, or temperature...
See MoreIntroduction to Noise Filtering
Introduction to filtering - moving average, first-order, anti-aliasing, set point softening
See MoreFirst-Order Filters
Use data filters to temper noise - relation of options to lag and variance reduction
See MoreA Statistical Noise Filter
A noise filter that uses Statistical Process Control (SPC) techniques to temper tampering
See MoreScaled Transmission Signals, Engineering Units, and Conversions
Information is transmitted in scaled signals (4-20 mA, 3-15 psig, 0-100%, digital counts), which are also deviations from some reference vales (such as psi gage is to psia). But process...
See MoreInterpreting Lines on PFDs and P&IDs
Lines on a process flow diagram (PFD) indicate material flow. In contrast, on a piping and instrument diagram (P&ID), the control overlay for the PFD, the lines represent information flow. ...
See MoreControl Valve Problems
Control valve problems can severely affect control loop performance and, unless eliminated, they can make controller tuning a challenging (sometimes impossible) task. Some problems are quite...
See MoreGain Scheduling (Pre-programmed Controller Parameter Adjustment)
Process gain and time-constants change with operating flow rate, tank levels, temperatures, etc. This often requires re-tuning of the controller coefficient values. However, once done...
See MoreNonlinear Control Output Signal Characterization
If the process gain makes large changes over the operating range, then tuning PID (or other linear) controllers is difficult. If tuned for one region, the controller is undesirably sluggish...
See MoreOutput Characterization to Linearize a Loop - Control valve application
This application paper explains how a control valve created nonlinearity in a loop and how output characterization solved the problem
See MoreOverride and Reset Feedback
Override controllers are for safety or switching to auxiliary variables. The non-selected controller needs to prevent becoming wound up.
See MoreRatio Control - the right and wrong approach
A discussion as to why the ratio should be the MV (controller output) not the CV.
See MoreRatio Control and Scaled Signal Calculations
When and how to use Ratio Control and use Scaled Signals
See MoreCascade Control
When and how to use Cascade Control
See MoreCascade Control
What is Cascade Control and why use it?
See MoreCascade Control 2
An Implementation Recipe for Cascade Control
See MoreFeedforward Control
When a Ratio Control strategy takes action too soon, use Feedforward to temper the dynamics. When a disturbance can be measured, but would not be a ratio of the control output use...
See MoreFeedforward Control
When and how to use Feedforward Control
See More